OFFSHORE MATERIALS COORDINATOR JOB DESCRIPTION
Find detail information about offshore materials coordinator job description, duty and skills required for offshore materials coordinator position.
What does a material coordinator do?
The responsible for the coordination, organization and issuing of inventory within a work cell or group of products. They will process job materials, back ordered materials, DMR materials & Job Traveler packages to fulfill production requirements.
What is a material administrator?
When it comes to purchasing, a materials manager is responsible for overseeing all aspects of the process. They research best prices and monitor inventory levels to ensure that supplies are always available and affordable. Additionally, they work with suppliers to negotiate contracts that are fair for both parties.
What is material coordination?
A material coordinator is responsible for managing the flow of materials and supplies in a construction, distribution or manufacturing setting. They are responsible for accurate and timely shipping as well as ensuring that materials are used efficiently. This position can be found in many industries, so it is important to have a strong understanding of the various sectors in order to be successful.
What are the skills required in a material manager?
A materials manager is responsible for managing the materials needs and inventory of a company. They work with the suppliers to procure the necessary supplies and make sure that products are delivered on time. Additionally, they are responsible for forecasting and budgeting to ensure that the entire project is met. In order to be a successful materials manager, you must have experience with both shipping and receiving as well as supply chain and inventory management systems. You must also be proficient in Microsoft Office. This position requires excellent organizational skills and leadership abilities.
What degree do you need to be a Materials Manager?
Many materials managers start their career by majoring in business administration, logistics, or management. These fields allow for a strong understanding of how businesses function and how to manage resources. In addition to this knowledge, material managers must also have an excellent eye for detail and be able to think outside the box when it comes to solving problems.
What is the difference between material management and supply chain management?
A supply chain is a network of businesses that are involved in the provision of product and service packages to end customers. The most important part of a supply chain is the material management branch, which deals with the tangible components of a supply chain. This includes everything from packing materials to crates of products.
Is material coordinator a good job?
Material coordinators are responsible for coordinating the manufacturing and shipping of products. They may also be responsible for providing customer service or overseeing production. This career can provide a lot of financial stability, so it is important to have the correct skillsets in order to succeed. In order to be a successful material coordinator, you will need to have excellent customer service skills, as well as experience with logistics and manufacturing.
Who is logistics coordinator?
The logistics coordinator is responsible for the smooth and efficient distribution of products in a company. They ensure that the products are delivered to their destination in a timely manner, and that all necessary permits are obtained before distribution begins. The coordinator is also responsible for ensuring that product safety is always considered when distributing products.
What is the store keeper job description?
In order to keep the store run smoothly, store keepers are responsible for ensuring that all inventory is properly cataloged and inventoried. Additionally, they are in charge of managing the store layout, ensuring that everyone is getting the most out of their space.
What is procurement coordinator?
A procurement coordinator oversees the purchasing of materials for an organization. They are responsible for ensuring that all necessary supplies are purchased in a timely and cost effective manner. They also work to ensure that the correct products are chosen for the needs of the organization.
What is SAP MM module?
SAP MM is a module of the SAP ERP software package from SAP AG that is used for Procurement Handling and Inventory Management. It covers all tasks within the supply chain, including consumption-based planning, planning, vendor evaluation and invoice verification.
Who is responsible for material management?
Purchasing managers and buyers in businesses must compare prices and determine the quality of products to build products or sell to customers.
What is material handling experience?
A material handler is responsible for moving goods around in warehouses and production facilities. They may also put products on delivery trucks and take them off of trucks to put them on shelves. The handler's job is important because it ensures that customer orders can be fulfilled quickly.
What is the meaning of material management?
Materials management is the process of controlling all material and equipment so that they are requested in advance, obtained at a reasonable cost, and are available when needed. This definition includes not only materials that go directly into construction projects, but also supplies and tools that are used in the construction process.
Is material management part of logistics?
Inventory management is essential for companies that depend on raw materials, machinery, and maintenance to function. It is crucial that processes reliant on these items are well organized and managed so that shortages or over-runs can be avoided.
What are the 4 types of inventory?
Inventory is a critical component of any business. It allows businesses to track what they have and how much they need, and it can help them plan for future needs. There are four main types of inventory: raw materials/components, WIP, finished goods and MRO. Raw materials/components are the most basic type of inventory. They are things like metals and plastics that businesses need in order to produce their products. WIP is the amount of work that needs to be done in order to make a product, typically refers to the amount of work that needs to be done in order to create a prototype or design. Finished goods are the finished products that businesses produce. This might be things like clothing or shoes, or it might just be an item like a computer keyboard. MRO is another type of inventory, which is meant for making money. This might be something like software or an online store.
What are the five major areas of materials management?
Strong leadership and strong materials management systems help ensure a successful launch. Leaders understand the importance of good materials management and are committed to ensuring everything is properly handled and organized. This allows for a smooth launch process and greater organization overall.
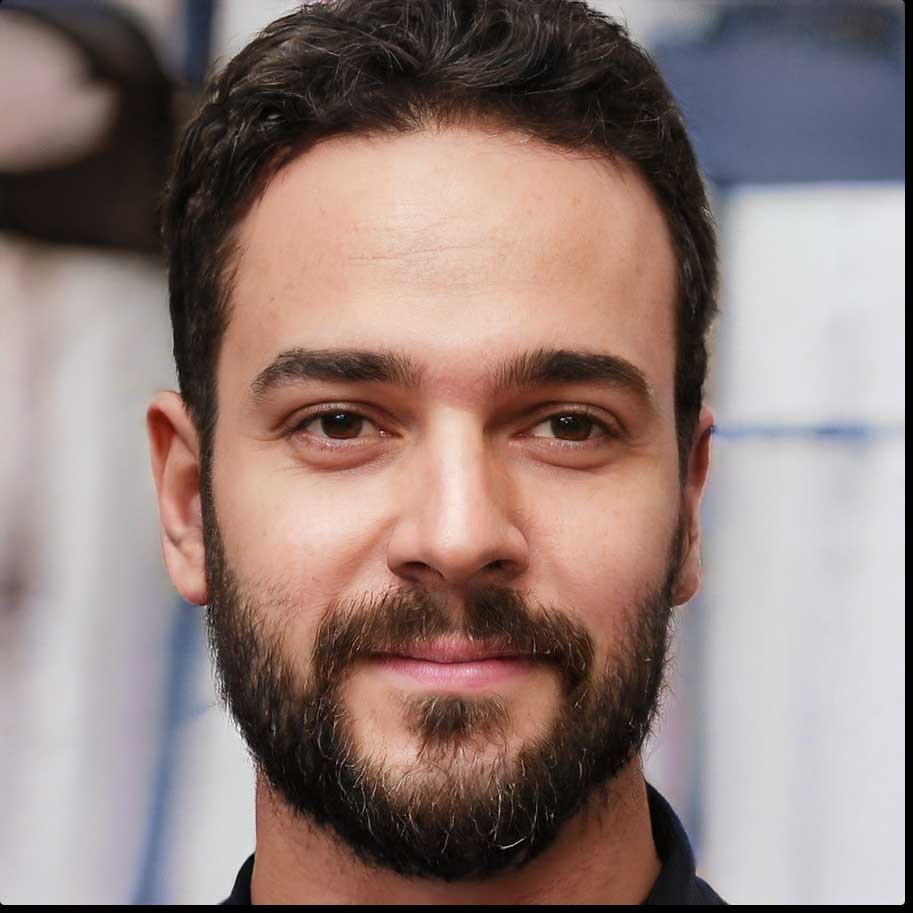
Warning: Undefined variable $post_category in /var/www/bestcareerguide.com/post.php on line 96
Category