MATERIAL CONTROL JOB DESCRIPTION
Find detail information about material control job description, duty and skills required for material control position.
How do I become a material controller?
As a material controller, you will be responsible for controlling the flow of materials through your company. This can involve managing stock, overseeing shipments, and keeping accurate records. In order to be successful in this job, you must have experience with various logistics systems and be able to communicate effectively with other employees.
What is a material control manager?
The Materials Control Manager is responsible for coordinating the distribution of materials for production. They analyze materials and determine what level of control is necessary to produce the desired outcome. This position typically reports to a head of a unit/department.
What is a crypto material controller?
The material controller coordinates the movement of materials between departments in a company. This position's duties include creating records of materials' movements in the company, negotiating with vendors, carrying out safety checks, and ensuring operations follow company and industry regulations. The material controller is responsible for ensuring that all materials are moved safely and efficiently within the company.
What is material control and its objectives?
Material control is the key function of a company that manages its materials so that they are used efficiently and without waste. This can be done by ensuring that materials are stored safely and properly, checking their handling when received, and accounting for any losses.
What is the store keeper job description?
The store keeper is responsible for keeping a record of sales and restocking the store accordingly. They are also responsible for managing and training store staff. They also plan promotional campaigns for new products or specials. The store keeper is also responsible for ensuring that the store is kept clean and organized.
What are the skills required in a material manager?
A materials manager is responsible for overseeing and managing the storage, handling and delivery of materials to and from businesses. They also have a responsibility for forecasting inventory needs and ensuring that products are delivered on time. This position may require some coordination with other departments within the company, as well as knowledge of SAP MM. The materials manager must be able to work independently and be able to manage multiple projects at once. They should be able to respond quickly to changes in inventory or demand from customers.
What is SAP MM module?
SAP MM provides companies with the ability to manage materials, inventory and warehouse operations. This module provides companies with a variety of tools and options to help them manage their needs, from inventory management to material tracking.
What is the responsibility of production control?
A factory manager is in charge of the staff and activities involved in the production of goods. They ensure production lines run smoothly and efficiently. They are responsible for ensuring that all products are made to order, and that all deadlines are met. A factory manager has a lot of control over how products are produced, and they can use their discretion to ensure that the products they produce meet customer needs.
What are the types of material control?
Usually, material management experts work on projects that require a great deal of resources and might even require the use of hazardous materials. They must plan for all eventualities and make sure that the resources they use are accessible and healthy. They must also keep track of all available materials and keep them organized in an efficient manner.
Why material control is important?
Materials control is one of the key aspects of any business. By ensuring that the stock of raw materials is within limits, it ensures that proper storage is done and that the necessary parts are made when needed. This helps to ensure a high quality product when finished.
What are the two levels of material control?
Most people believe that financial control is the most important control for any business. This is because it allows a person or company to regulate how much money they spend, and how much money they make. Financial control can be used to manipulate people or companies, so it is an important tool for any business.
How much is the salary of a storekeeper?
The Store Keeper in Nigeria is a vital part of the society and their job is often difficult. They are responsible for stocking the store with the latest in clothing, cosmetics, kitchen supplies, and other necessary items. They can earn a monthly salary of 154,000 NGN which includes housing, transport, and other benefits. With such a high wage it is no wonder that these employees are often very healthy and happy.
How do you interview a storekeeper?
When you helped a customer identify the best product for their needs, you were able to provide valuable feedback and help them find the perfect solution. You were able to handle stocking needs, including when to order new items. You also used methods to resolve scheduling conflicts with employees, which made life easier for them.
What is the qualification for store keeper?
Direct recruits must have at least three years' experience in the maintenance of stores ledgers and accounts. They must also have a degree in Science or Commerce from an approved organization. The direct recruit must be able to communicate effectively with customers and employees.
What is the difference between material management and supply chain management?
Materials management is the branch of logistics that deals with the tangible components of a supply chain. By understanding and following simple principles, SCM can help manage your material inventories and ensure that you have enough products to meet demand. By following these simple tips, you can create a successful material management system for your business.
What is material handling experience?
The Material Handler helps keep the workplace clean by delivering or opening products for clients. They also maintain in-process inventory at work centers by delivering or opening products for clients.
Who does a materials manager report to?
The Materials Manager oversees the day-to-day performance of subordinate staff in the Department of Materials Science and Engineering. The Materials Manager manages a wide range of materials including, but not limited to, metals, plastics, and composites. The Materials Manager is responsible for ensuring that all materials are used in accordance with departmental and university policy. In addition to their duties as Materials Manager, the Material Manager also oversees budgetary procedures and works with the Head of Unit/Department to ensure that all necessary supplies are available when needed.
Which SAP course is best?
There are many high-paying SAP modules out there. SAP S/4HANA is one of the most popular SAP modules, and it can be used to create powerful analytical reports and understand your business better. Additionally, SAP ECC FI is a great module for financial accounting. SAP SCM can be used to manage your supply chains more efficiently. Finally, SAP HCM is perfect for human capital management. With these three modules, you will be able to create powerful reports that help you understand your business better and make better decisions.
What is the job description of quality control?
Inspecting output samples is a critical part of the quality control process. By using industry-appropriate methods, you can ensure that the assembly or production line follows standards and meets legal requirements.
What is a controller in manufacturing?
A manufacturing cost controller assesses and ensures that the overall manufacturing process meets the needs of the firm. The job of a manufacturing cost controller is similar to that of budgetary control--in which actual costs incurred by an organization are compared with allocated resources. A cost controller examines all aspects of the manufacturing process, from product development to shipment, in order to ensure that costs are within budget. This allows for proper allocation of resources and increased efficiency in the business.
Why quality control is to be done?
Quality control procedures at a company can help ensure the quality of products being sold. This can inspire employees to create high-quality goods, leading to increased customer satisfaction. Practices such as quality control can also help prevent incidents from happening, which in turn can improve the overall business climate.
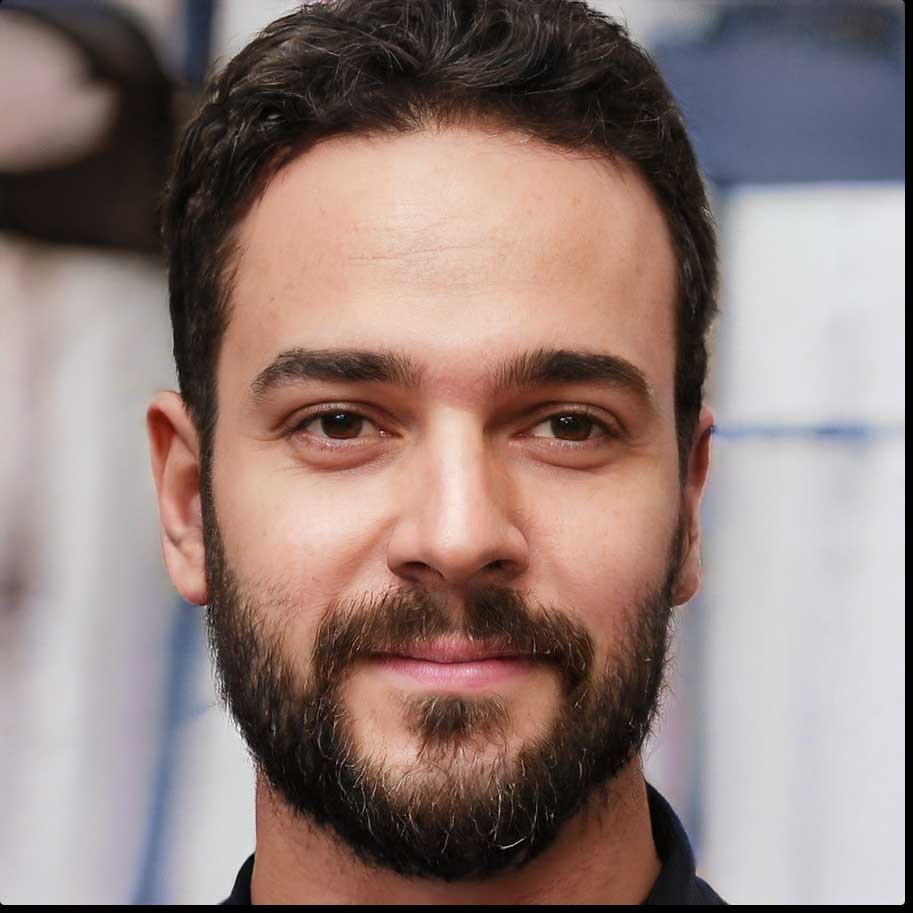
Warning: Undefined variable $post_category in /var/www/bestcareerguide.com/post.php on line 96
Category