MATERIAL COORDINATOR JOB DESCRIPTION
Find detail information about material coordinator job description, duty and skills required for material coordinator position.
What are the duties of a material coordinator?
A coordinator oversees the inventory of products and materials for a company. They inspect shipments and handle requests for maintenance. Coordinators are responsible for a broad range of tasks related to product management and oversight.
What is a material administrator?
It is a responsibility of a materials manager to ensure that company's inventory and purchasing departments are coordinated. They must research the best prices and monitor inventory levels to ensure that supplies are distributed evenly. Additionally, they must negotiate contracts to ensure that products are furnished at the best prices.
What is procurement coordinator?
A procurement coordinator oversees the purchasing of materials for an organization. She is responsible for ensuring that all necessary supplies are ordered and purchased in a timely manner, and that the best possible prices are attained for each item. This can be important for any business, as often times there are tight budget constraints.
What is a raw material coordinator?
Most businesses need someone to coordinate all of their inventory. The Material Coordinator is responsible for procuring goods and services such as raw materials, equipment, tools, parts and supplies, and purchases all inventory to meet production goals. This person is also responsible for ensuring that all products are of the correct quality and meet customer needs.
Who is logistics coordinator?
The logistics coordinator is responsible for the overall coordination of a supply chain. They work to ensure that products are delivered in a timely and efficient manner, and that the products are of good quality. This position may also include managing resources, such as Inventory, Shipping, and Distribution.
What is material handling experience?
Material handlers move products around quickly and accurately, making customer orders easily fulfilled and moved quickly. They are a vital part of the supply chain, handling materials that make up everything from clothing to food.
What are the skills required in a material manager?
Nina is a passionate person who loves to help others. She has more than ten years of experience working in the supply chain and inventory management field, and she knows how to manage and forecast inventory levels in order to keep the business running smoothly. Nina's past experiences have taught her how to work well with other team members, and she is an excellent communicator and leader.
What degree do you need to be a Materials Manager?
A materials management job in healthcare is a challenging and rewarding position. The job requires a four-year degree from a regionally accredited college or university, but it can be done in a number of different fields. For example, a materials manager could major in business administration, logistics, supply chain management, or management. This position can be extremely helpful to businesses because it allows them to manage their resources effectively and efficiently.
What is procurement job description?
The procurement officers in a company are responsible for evaluating suppliers, products, and services, negotiating contracts, and ensuring that approved purchases are cost-efficient and of high quality. They are also responsible for making sure that the products they select are the best possible options for the company.
What is term procurement?
Business procurement can be tricky, but it's an essential part of any company. Preparation and payment processing are essential to making sure that the purchase is completed efficiently and without any issues.
What are the duties of a procurement specialist?
Most companies require a procurement specialist to help them meet all of their specifications. This person is responsible for finding key suppliers and negotiating purchasing agreements with them to get the best quality goods at the lowest prices possible. By working closely with these suppliers, companies can save a lot of money on their products.
Is logistics coordinator a hard job?
A logistics coordinator is someone who is responsible for overseeing the flow of goods and materials through a company or organization. They need to be able to work with others in a quick-paced environment, able to think on their feet and manage multiple tasks at once. This position does not require a college degree or advanced technical knowledge.
Is logistics coordinator a good job?
A logistics coordinator is a key member of any business. They are responsible for ensuring the safe and timely delivery of purchase goods. The job is highly stressful, but with the right tools, it can be a rewarding experience.
What are the interview questions for logistics coordinator?
A typical day for a logistics coordinator may involve attending meetings, coordinating the delivery of goods, and managing purchasing. They may also be responsible for determining the necessary resources to complete a task and ensuring that deadlines are met.
Is material handler job hard?
working at FedEx is a very stressful experience. You are constantly responsible for others and must be quick to come up with solutions to problems. This can be a difficult task when it's a nightly issue.
Is material handler hard?
Some employers may require certain physical abilities, such as being able to lift 30 pounds or participating in team lifts of items 40 pounds or heavier. Some handlers may find it difficult to do these strenuous tasks without experiencing pain. This can be a challenge for handlers who do not have the proper training or equipment.
What is material handling in warehouse?
In a warehouse environment, material handling is a critical process that ensures the safe and efficient movement of materials and products throughout manufacturing. The manual, semi-automated and automated equipment and systems play an important role in this process, moving materials and products at the correct speed and ensuring that all material is handled safely.
What is the difference between material management and supply chain management?
In business, supply chain management (SCM) is the management of a network of interconnected businesses involved in the ultimate provision of product and service packages required by end customers. SCM is responsible for managing materials in the network, ensuring that products are delivered on time and in the required quantity.
Who reports to the Materials Manager?
In a materials management environment, it is critical to work closely with product line coordinators on the planning and forecasting of customer orders. This ensures that shipments are completed on time and within budget. Additionally, Materials Manager typically reports to a Head of a Unit/Department. In this role, you will be responsible for managing materials used in products and ensuring they are consistent with production standards.
What is the meaning of material management?
Construction companies are always looking for new and innovative ways to improve their materials management. By using advance planning and efficient procurement, they can ensure that their workers receive the best possible equipment and supplies at a reasonable price.
How can I be a good material controller?
The employee is a pro-active nature and is always willing to learn. She is also appreciative of good in/stores disciplines. She is attentive to detail and has good interpersonal skills. The employee also has health and safety awareness in the warehouse environment.
How do I become a material controller?
material controllers are responsible for managing and controlling the flow of materials through a company. They work with other parts of the organization to ensure that all materials are accounted for, moved, and stored in a safe manner. They must be aware of safety regulations and be able to communicate effectively with others.
Which is part of material management?
Materials management is an important process that oversees the flow of materials throughout an organization. This includes planning and controlling material flows, supplier evaluation and selection, purchasing, expenditure, shipping, receipt processes for materials (including quality control), warehousing and inventory, and materials distribution. By communicating plans and ensuring that all necessary steps are taken to ensure the safekeeping of materials, you can minimize any potential risks associated with their use.
Is procurement a stressful job?
Procurement professionals are faced with a high degree of stress because of the demands made on them to meet deadlines, assess needs and deliver on promises. This type of stress can lead to burnout, which can impact worker productivity and morale.
Why do I want to work in procurement?
A procurement officer is a key player in the Purchasing and Supply Chain Department of any company. They are responsible for allocating resources to projects, monitoring the projects, and ensuring that all stakeholders are meeting their agreed-upon goals. A procurement officer is known for their high visionary and goal-minded traits. They are constantly looking for ways to improve the purchasing process and make better decisions for their companies. This means they are always seeking ways to save money, improve efficiency, or deliver better results.
What to study to become a procurement officer?
As a procurement specialist, you will be responsible for planning, conducting and managing procurements. By understanding the different aspects of procurement, you will be able to make informed decisions that benefit your company and its customers. As a procurement specialist, you will need to have strong math skills as well as strong writing skills in order to communicate with potential and current customers.
What are the 3 types of procurement?
Fixed-price contracts are the most common type of contract. They specify a fixed price for the project and the contractor is responsible for paying it on time. This type of contract is often used when there is a tight deadline or there are specific instructions that must be followed. Cost-reimbursable contracts are similar to fixed-price contracts but they allow the contractor to pay themselves back over time. This type of contract is often used when there is a more skeleton crew and the contractor doesn't have to worry about paying everyone on time. Time and materials contracts are also similar to fixed-price contracts but they allow for different payment schedules or periods of time that the contractor must complete the project. These types of contracts can be Useful when contractors have specific deadlines or require a certain amount of work before they begin billing.
What are the 3 types of purchasing?
A purchase is a formal act of contracting to transfer goods or services between two people or organizations. In most cases, the two parties involved in the transaction will be known as buyers and sellers. Purchases can take many forms, from purchasing a single item to purchasing entire assemblies of products or services. Mercantile purchases are transactions where goods and services are bought and sold between two companies, banks, or other financial institutions. Mercantile purchasing often occurs in industries that produce large quantities of goods and services that need to be moved around quickly, such as transportation, food manufacturing, and logistics. Industrial purchases are transactions where goods and services are bought and sold between businesses that produce a specific kind of product or service. This could include companies who make cars, computers, pharmaceuticals, or other products that need to be marketed specifically to a certain market. Industrial purchasing is often done in industries that have high demand but low production costs. Institutionalized or government purchasing is a type of purchase where money is transferrable from one person or organization to another without involving any physical action on the part of either party. This type of purchase can be used for things like buying supplies for an upcoming business meeting or providing administrative support
What are the 7 stages of procurement?
The 7 procurement process steps involved in procurement management process are: 1. Needs Recognition. 2. Purchase Requisition. 3. Requisition review. 4. Solicitation process. 5. Evaluation and contract. 6. Order management. 7.Invoice approvals and disputes
How can I be good at procurement?
Every procurement specialist should have the 10 skills listed below in order to Holistically Manage Risk, Sustainability, Improve Supplier Relationships, Participate in a Global Market, Involve New Technology, Develop Financial Procurement Specialist Skills and Lead in Innovation.
What are procurement skills?
procurement skills are the abilities that purchasing managers or procurement specialists use to guide purchasing decisions within a department or business. They use communication, business and research skills to determine what equipment or material is best for daily functions or projects.
How do you write a procurement resume?
"I am a procurement professional with over 10 years of experience. I have the ability to work independently and as part of a team. I am a strong writer, and I have a history of taking on complex procurements. My skills include: - Proven experience in both purchasing and contracting - Strong attention to detail - Excellent communication, writing, and problem solving skills - stamina - Ability to learn new things quickly" - source.
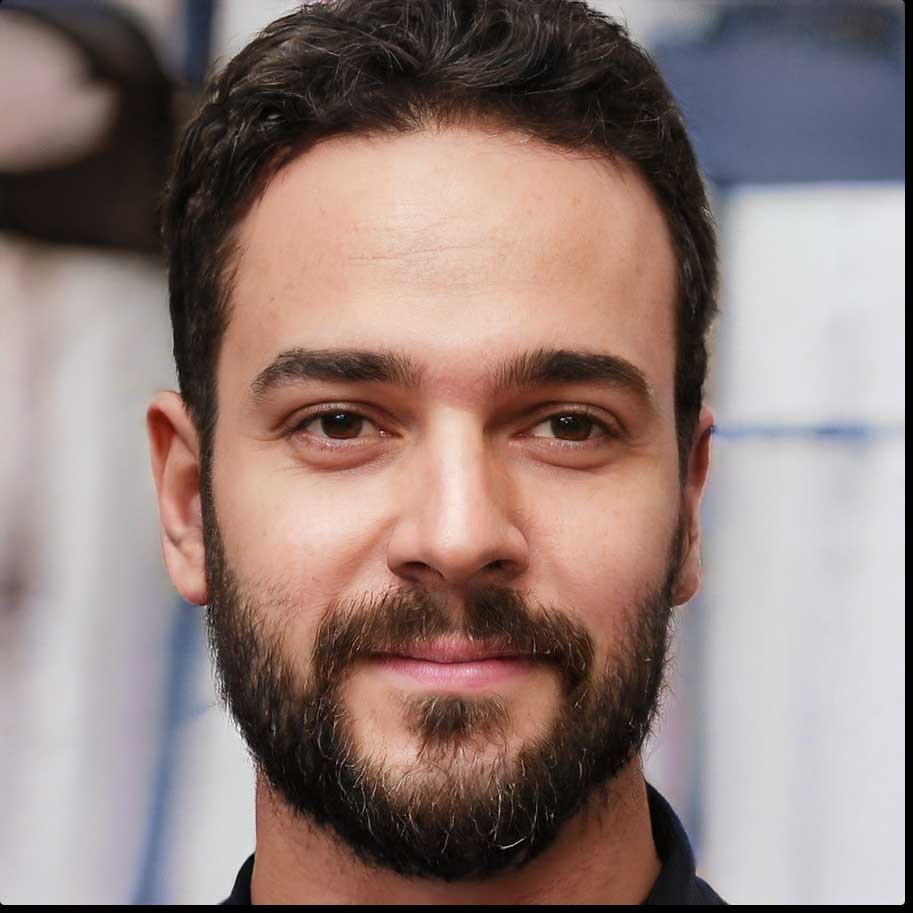
Warning: Undefined variable $post_category in /var/www/bestcareerguide.com/post.php on line 96
Category