QUALITY CONTROL MANUFACTURING JOB DESCRIPTION
Find detail information about quality control manufacturing job description, duty and skills required for quality control manufacturing position.
What is the role of quality control in manufacturing?
In the manufacturing process, quality control is a key step that ensures customers receive products that meet their needs. When done incorrectly, it can put consumers at risk. For example, if a manufacturing worker makes a mistake with an ingredient, this could lead to a product that is not safe to use or could even be dangerous. This could lead to customers being injured or even killed.
What is quality control in a job?
Quality control is a process through which a business seeks to ensure that product quality is maintained or improved. Quality control requires the company to create an environment in which both management and employees strive for perfection. In order to ensure that the products they produce are of high quality, businesses typically use QC methods such as testing, inspection, and verification. This process ensures that the products are safe and meet customer requirements.
What are the 5 types of quality control?
Seven quality control tools are important to any business. Fishbone diagram, control chart, stratification, pareto chart, histogram, and scatter diagram are all important tools for ensuring quality.
What are the 3 main objectives of quality control?
In a quality control system, three goals are to ensure product quality and reduce risks, gain production efficiencies, and garner customer loyalty. By enhancing product quality and reducing risks, the company can save money and increase profits. Additionally, by gaining production efficiencies, the company can improve efficiency and make more money. Finally, by using customer loyalty as a motivator, the company can keep customers happy and stay strong in the market.
Is quality control a good job?
Do you have experience working with QC analysts? If so, this may be the perfect role for you! As a QC analyst, you will be responsible for performing a variety of tasks which will provide you with a broad range of experience. This is an excellent opportunity to begin your career in industry and gain valuable skills that can be transferred into future positions.
What are 4 types of quality control?
Four types of quality control are process control, acceptance sampling, control charts, and product quality control. Process control is the use of specific methods to ensure that the products produced meet the required standards. Acceptance sampling is a technique used to measure the levels of product quality before they are released to the marketplace. Control charts are a graphic representation of the flow of material through a manufacturing process. This type of control can help managers track progress and make changes as needed. Product quality control is the monitoring and assessment of products to ensure that they meet customer expectations.
What is the salary of quality control officer?
Quality Control Officer (QCO) in India is a highly paid and prestigious job. The average annual salary of a QCO in India is 3.1 lakhs. This is a very good salary for someone who wants to work in the field of quality control.
What are 3 examples of quality control?
Quality control activities are important in any organization. They ensure that the products and services that are delivered are of good quality, and that no errors occur. In a company, there are many different tasks that need to be done to ensure the quality of products and services. These tasks might include inspection, peer reviews, and software testing. Each task has its own set of risks and benefits, so it is important to choose the right one for the specific situation. Inspection is important because it can help identify any problems with the product or service. Peer reviews can help us identify how well the product or service is working. Software testing can help us find any errors that may have occurred in the product or service.
How can I be quality control?
6 steps to develop a quality control process: 1. Set quality standards. Everyone needs to set their own quality standards in order to maintain a high level of quality in their work. 2. Decide which quality standards to focus on. It is important to focus on specific areas that need improvement, so you can improve the overallquality of your product or service. 3. Create operational processes to deliver quality. This will help ensure that the quality of your product or service is consistent at all times. 4. Review your results regularly and make changes as needed. This will help you track progress andperfect your process every time! 5. Get feedback from users and other stakeholders in order to learn what works and what doesn't work in order to improve thequality of your product or service further. 6. Make improvements as needed based on user feedback and successful practice
What are the 2 types of quality control?
Some quality control methods used in manufacturing are inspection, process inspection, and inspection analysis.
What is quality control in simple words?
QC is a process or set of procedures intended to ensure that a product or service meets the requirements of the client or customer. QC is similar to, but not identical with, quality assurance (QA). QC is important for products and services that are sold to the public, as well as those that are used within the company.
What is quality control a level?
Quality control is a vital part of any business. It ensures that products meet the required quality standards and that everyone who uses them is safe. This process checks the quality of completed products for faults, ensuring that they are perfect in every way.
What is the main aim of quality control?
Quality Control is a process that is used to ensure the quality of products. This process includes reviews of products by other members of the company, as well as testing and checking of products to make sure they are safe.
What degree is needed for quality control?
A quality control inspector is responsible for inspecting products to ensure they meet specific standards. They may also be called upon to inspect the work process itself, to monitor the results of other inspections, or to help ensure that products meet specific safety requirements.
How do I start a career in quality control?
Quality assurance analysts and inspectors often have a background in engineering or other science. They use their knowledge to ensure the quality of products and services. Some basic requirements for aquality assurance analyst or inspector include a Bachelor's degree in an appropriate field, as well as certification from an industry-standard body.
What degree do you need to work in quality control?
Entry-level quality control inspectors should have at least a high school diploma or equivalent. Having a bachelor's or associate degree in quality assurance can expand a quality control inspector's job opportunities and increase their earning potential. They should be experienced in inspecting materials, products, and services to ensure that they meet specific standards.
What are quality standards in manufacturing?
The ISO 9000 quality standard is a set of good management practices, methods, systems, requirements, and/or specifications that help manufacturers achieve and demonstrate consistent production and product quality. The standard was created to help companies stay up to date with the latest technology and improve their efficiency.
What are the 3 types of quality?
Quality is a main factor that customers take into account when choosing an industry or product. It can be described in three ways: performance, excitement, and excitation. Performance quality refers to the level of quality that an industry or product can provide. This could be referring to how well the product performs, how quickly it arrives, or what other features are included. Excitement quality refers to how great the product makes customers feel and how exciting it is to use. This could be referring to everything from products that give you a heart attack when you try them, to products that make you feel like you are having a great time. Excitement is important because it creates the feeling of satisfaction andtrust in an individual product or industry.
What are the documents required for quality control?
ISO 9001:2015 requires all organizations to develop and maintain a quality policy, achieve objectives, and keep records of training, skills, experience, and qualifications. Organizations must also review product/service requirements to ensure that they meet customer needs.
Which is better QA or QC job?
Good quality control ensures that all products are of the same quality and that no mistakes are made. This helps to ensure that the product is of good quality and can be used successfully.
What is a quality control job description?
The quality control inspector is responsible for ensuring the quality of products and materials entering and leaving a company. They may also be responsible for conducting tests to ensure the product is of acceptable quality, analyzing products, and overseeing production procedures.
What are the 4 types of quality control?
Quality control is a method of ensuring the quality of a product. This includes an x-bar chart, Six Sigma, 100% inspection mode, and the Taguchi Method. The Taguchi Method is a process that uses pairs of products to test different aspects of each. This allows for comparison and discovery of problems.
Is quality control a good career?
In the manufacturing industry, quality control and assurance professionals are essential for ensuring the quality of products. They need to be able to see the big picture, be able to plan and organize, and have strong communication skills. They also need to be able to work with other people, and be able to problem-solve.
What is the qualification for quality control?
The Quality Control Personnel are responsible for ensuring the quality of goods and services supplied to the customer. They possess a degree in a related field and experience in working with customers.
What are quality control skills?
A company's quality control system is a layer of management that ensures the quality of products they produce. The system includes standardizing processes and assessing product performance to make sure it meets safety and quality standards. Standards are set for materials, manufacturing processes, and finished goods. The company's quality control system must ensure that products meet safety and quality standards. This includes setting specific standards for materials, manufacturing processes, and finished goods. The company must also be able to assess the product?s performance to make sure it meets these standards.
What are the 3 types of quality control?
Most manufacturing plants require a variety of quality inspections in order to detect and correct quality problems. Pre-production inspections may be needed to ensure that the product is of the correct size, shape, color, etc. In-line inspections are used to verify that the product is being produced as planned and that all tolerances are met. Final inspections may be used to ensure that all products have been completed properly and any defects have been corrected.
What is quality control Example?
One of the ways that quality control is important is by ensuring that all products are made correctly and that they meet the specific needs of the customer. This process begins by inspecting each product to make sure it is properly made and then testing it to ensure that it meets specific needs.
How do you perform quality control?
1. Set your quality standards. 2. Choose which quality standards to focus on. 3. Create operational processes to deliver quality. 4. Review your results. 5. Get feedback. 6. Make improvements
Why do you want to work as quality control?
"I enjoy working in quality because it's an industry where you can really make a difference. You can increase profitability for businesses and at the same time ensure products are safe and meet or exceed consumer expectations. My favorite part of the job is being able to see results from my work, as I am able to help contribute to the success of my employer." - source.
How do I create a career in quality control?
Usually, when looking for qualities that are essential in a quality manager, it is important to focus on the following three qualities: listening skills, self-confidence and patience. Listening skills are vital in the quality management industry because they are the first step to effective problem-solving. As a quality manager, it is your obligation to be able to listen attentively to your clients and colleagues, in order to get a clear understanding of their needs. Self-confidence is another essential quality for a quality manager. A good self-belief will help you stay calm under pressure, which is key in facing difficult challenges. Additionally, patience is also necessary for high-pressure situations - being able to wait until the right time has come before making a decision can lead to success.
What is quality control team?
A quality assurance team conducts activities that validate quality requirements. This typically involves planning, observation and inspection. The team's goal is to ensure that products or services meet customers' expectations and that there are no discrepancies. This process can help to ensure the accuracy of product data and the quality of service provided.
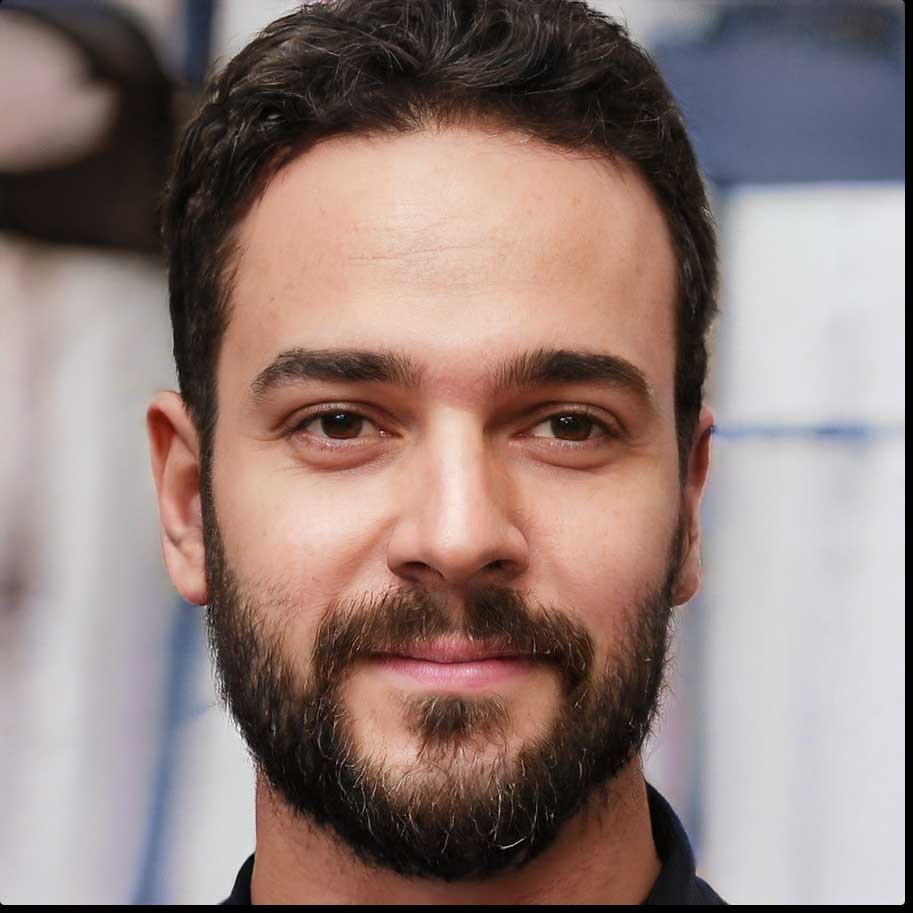
Warning: Undefined variable $post_category in /var/www/bestcareerguide.com/post.php on line 96
Category