PARTS INVENTORY SPECIALIST JOB DESCRIPTION
Find detail information about parts inventory specialist job description, duty and skills required for parts inventory specialist position.
What does a inventory specialist do?
Usually, the Inventory Specialist is a professional responsible for checking shipments going in and out of the company and ensuring that all orders are delivered correctly. They must also report any issues with inventory management systems or other employees to their managers so they can resolve these problems quickly. The Inventory Specialist is always working hard to ensure that all orders are delivered correctly, and if there are any problems with either the systems or employees, they must report this to their managers so that solutions can be implemented as quickly as possible. This is an important role in ensuring that the company's smooth operations, and it is something that they take seriously.
What are the skills of an inventory specialist?
She has a background in mathematics, ERP and data entry systems, and is comfortable working with large quantities of data. She is also a good communicator, able to write creative and descriptive English sentences.
What do you do in an inventory job?
The custodian of the store is responsible for maintaining and updating records. They must also count materials, equipment, merchandise or supplies in stock. They are also responsible for reporting discrepancies between physical counts and computer records. The custodian is also responsible for receiving and inventory stock.
What industry is inventory specialist?
Inventory specialists are responsible for ensuring that products are ordered and placed in a timely manner. They count products to ensure accuracy and keep track of what is currently in stock. This can lead to improved efficiency when running a store. Inventory specialists can also be creative with their ideas and come up with new ways to improve the store's operations.
How can I be a good inventory specialist?
A successful inventory specialist must have excellent interpersonal communication skills, a firm grasp of basic computer programs, and an ability to work both independently and in a team. Ideal candidates will have inventory experience as well as mid-level management experience.
How do I get a job in inventory management?
The ideal candidate for a supply chain management position would have at least five years of experience in the field, working with inventory management software and forecasting strategies. They would also be able to conduct tracking and data analysis. In addition, they would need to be comfortable working with English language and be able to read and understand complex reports.
What is an inventory position called?
The Inventory Clerk is responsible for the organization and tracking of goods and supplies in a store or warehouse. They may also manage orders to facilitate sales or production. The Inventory Clerk is an important part of the store or warehouse management team, and their job is to ensure that all the goods and supplies are properly labeled, organized, and kept track of.
How do you put inventory on a resume?
The Inventory Manager is responsible for the administration and management of inventory on a company's premises. They must be able to work independently and provide leadership and guidance to their team. The Inventory Manager will be responsible for setting goals, managing resources, and developing policies.
How do I become an inventory analyst?
Inventory analysts are responsible for managing and analyzing physical inventory in a company. They work with other team members to identify and track inventory needs, determine when and how to order goods, and make sure products are delivered on time. Inventory analysts have a strong understanding of business concepts, including supply chains, demand management, and inventory management.
Is inventory control a skill?
Inventory controllers are responsible for ensuring the accurate and timely movement of inventory in a shop. This requires strong writing skills and knowledge of supply chains and inventory management. Inventory controllers must be able to read and understand stock levels, manage stock, create inventories, and communicate with other members of a store's staff.
Is inventory management a skill?
An inventory manager is someone who is able to keep track of inventory and make sure that it is always replenished. They also have to be able to communicate with other departments in order to get the most out of their work.
Why do we need to hire you?
"I have a wealth of experience in the field of advertising, having worked for major corporations such as Coca Cola and Pepsi. I am also an experienced author, having written articles for both online and print publications. My skills and experience go beyond simply writing; I have a full range ofanguages perfect for this position. I am confident that with my skills and experience, I can bring great value to your organization." - source.
What is inventory control in or?
Stock control is a critical function in any business. It ensures that the correct amount of product is available at the right time and prevents sales from falling behind. This can help to keep your business running smoothly and making money.
What is your experience with inventory management?
Inventory management is an important part of any business. It allows you to control how much inventory you have and how many products you can sell at a given time. It is also important for large businesses, where ERP software can be used. Inventory management allows you to keep track of what is in stock and what is being sold. This helps you make better decisions about what to sell and when to sell it.
What qualifications do you need to be an inventory clerk?
An inventory clerk is a type of worker who helps manage and stock inventory in a business. This job can be found in many different types of businesses, such as retail and manufacturing. An inventory clerk needs only a high school diploma or GED certificate, but many companies also seek candidates with several years of experience in the industry.
How do you describe inventory?
The sales team for a small business sells newspapers from a vehicle. The vehicle is used to deliver the newspapers to the customers. The sales team has inventory of the newspapers that they sell.
What skills do I put on a resume?
If you're looking to stand out from the crowd, you'll need to have some skills that differentiate you from the rest. Here are 20 must-have skills for a successful resume.
What is inventory clerk job description?
"The customer service representative was very helpful and polite. They were able to help me with my order and made sure that the order was delivered on time. The prices were very reasonable, too. Overall, I would definitely recommend this business to a friend." - source.
Do analysts make good money?
The median financial analyst salary is around $85,000, but this number can be misleading because the average financial analyst salary is closer to $100,000 due to the extreme growth in earnings over time. Financial analysts are highly sought-after professionals who play an important role in many businesses. Their skills and knowledge allow them to make significant contributions to companies by helping them understand complex financial problems and making recommendations for solutions.
What is product inventory management?
Inventory management is a critical function in any business. It ensures that your company has the necessary resources to meet its goals and objectives. It also helps to ensure that your inventory is properly stocked and used to meet demand. By ordering and storing your company's inventory, you can ensure that it is available when needed and at the best prices possible.
What are the 4 types of inventory?
Inventory is a vital process in a business. Raw materials, components, finished goods and MRO are all important when running a business. When it comes toinventory, it's important to have the right mix of each type to ensure your business is doing its best.
What are the interview questions for inventory management?
One of the most important aspects of running a business is managing inventory, and many businesses use inventory management systems (IMS) to achieve this goal. An IMS can help manage your inventory by tracking the stock levels and creating reports that allow you to track sales, cost of goods sold, and other performance metrics. An IMS can be used in a variety of ways, including Material Requirements Planning (MRP) systems. MRP systems are used to determine how much material you need to produce a product and then allocate that material among your manufacturing plants. By understanding how your IMS works, you can optimize your production process so that you produce the most efficient product possible.
What are your salary expectations?
I am looking for a salary range that would allow me to make a good living without breaking the bank. My ideal salary range would be from $73,000 to $80,000 per year.
How inventory is calculated?
Usually, the average inventory is a measure of the amount of sales that a company has in stock, and is used to compare different companies. In the case of this particular company, the average inventory can be used as a measure of their performance. By adding the inventory at the beginning of the period to the inventory at the end of it, and dividing by two, this company can then use this information to calculate their average inventory. This information can be used in order to determine how well they are doing against other companies in their industry.
What are the 2 methods of inventory control?
Inventory control is a key management tool that helps to keep your business running smoothly and efficiently. By controlling the stock of items, you can ensure that you have the necessary supplies available when you need them and that your customers have the products they desire. Manual inventory control is often more time-consuming and requires more effort than perpetual inventory control, but it can be a more accurate way to run your business.
What are the 3 main objectives of inventory control?
Inventory management is an important process for businesses in order to minimize holding, replacement and shortage costs. By minimizing the number of items in a product, businesses can increase efficiency and reduce the cost of production. Additionally, by stocking a larger variety of products, businesses can reduce the risk of having to purchase or produce a particular item that is not in stock.
Who is responsible for inventory control?
An inventory management solution can make your life much easier. An inventory system captures data on what is in stock, how much is left, and where it is located. This information can help you avoid overstocking items and keep your cash flow high.
What is a skill inventory?
The skills inventory compiled by the company is a valuable tool in assessing the skills of the current staff and future skill requirements. The inventory helps to plan strategic efforts, as well as identify any potential gaps in skills. The inventory also allows for comparison of employees against other staff members, to see which ones are best suited for the company's needs.
What is an inventory control analyst?
Inventory control analysts are responsible for ensuring the accuracy and completeness of inventory data, as well as improving the systems in place to manage this data. They also work to identify any discrepancies in sales data and recommend solutions.
What is inventory assistant?
When the Inventory Assistant is tasked with receiving parts, equipment, and materials to the warehouse inventory, they will do so in a highly organized and efficient manner. The Inventory Assistant will also be responsible for restocks for all division warehouses/vehicles. This individual is an essential part of any warehouse or dealership organization and should be well-trained in how to run the inventory process.
What are the 3 major inventory management techniques?
Manufacturers often use three different inventory management strategies: the pull strategy, the push strategy, and the just in time (JIT) strategy. The pull strategy is when a manufacturer pulls items from their production line in order to meet customer demand. The push strategy is when a manufacturer pushes products to meet customer demand in order to create a backlog. The just in time (JIT) strategy is when manufacturers place products into production as soon as possible so that they can sell them to their customers as soon as possible.
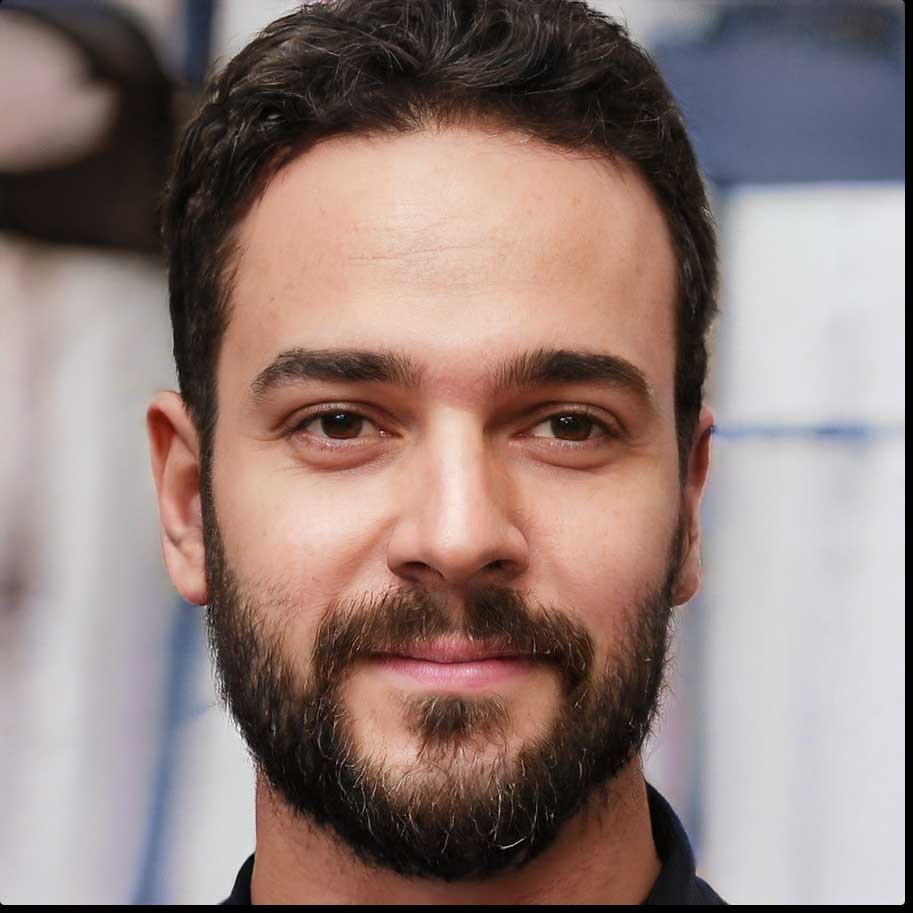
Warning: Undefined variable $post_category in /var/www/bestcareerguide.com/post.php on line 96
Category