MATERIALS SPECIALIST JOB DESCRIPTION
Find detail information about materials specialist job description, duty and skills required for materials specialist position.
What is a material flow specialist?
A manufacturing organization must manage the internal flow of material to support production requirements. This can include creating order backlogs, stocking materials, and managing shipping times.
What is a materials manager job description?
The Materials Manager will be responsible for the planning, procurement, storage, control, and distribution of materials and products according to company needs and customer requirements. They will work with different departments within the company to make sure that everything is coordinated and in line with company goals. The Materials Manager is also responsible for ensuring that all materials are safe and properly stored.
What is a BOM specialist?
The BOM Specialist is responsible for the development and maintenance of manufacturing BOMs and Routers in preparation for the business to transition into an Oracle ERP environment and to facilitate document change implementation in an aerospace production environment. The Specialist is also responsible for developing and maintaining blueprints and models of aircraft production systems.
What is a material administrator?
Most materials managers are responsible for managing the planning and coordination of a company's inventory and purchasing departments. They are tasked with researching best prices, monitoring inventory levels, distributing supplies, and negotiating contracts. They also have an important role in ensuring that materials are used efficiently and in the most effective way possible.
What degree do you need to be a Materials Manager?
A materials manager is responsible for the efficient and safe storage of materials in a hospital or other clinical setting. They must be able to think rapidly and organizedally as well as be able to communicate with other employees. Materials managers typically have a degree in business administration, logistics, or supply chain management.
What are the skills required in a material manager?
The materials manager is responsible for managing and organizing the company's vast Supply Chain resources. They must be able to understand and forecast inventory needs, as well as manage budgets. Additionally, they are required to have excellent organizational skills and be able to lead teams.
What is material handling experience?
Material handlers are responsible for organizing and verifying materials and supplies on production orders. They maintain in-process inventory at work centers by delivering or opening products for clients. Material Handlers also keep loading areas and machinery clean.
How do I become a good material coordinator?
One of the most important skills for a professional resume and career is creativity. By being able to come up with innovative solutions to problems and creating effective customer service, a person can stand out from the crowd. Additionally, having an inventory level that can handle changed demand and controlling expenses so that each expense is within budget are also important skills.
How do I become a materials coordinator?
Many companies require a degree in some form, but it is possible to become a material coordinator with a high school diploma. Experience as a customer service operator or material handler is often appreciated.
What is material executive?
The Materials Management Executive is responsible for all aspects of the purchase, storage, and distribution of raw materials, supplies, and equipment. They are also responsible for ensuring that inventory needs are met throughout the production process while maximizing the efficiency of warehousing and distribution operations. This individual is an essential part of any organization that produces goods or services.
Who does a materials manager report to?
The Materials Manager is responsible for the management of materials used in a company. This includes, but is not limited to, storage, inventory, and delivery. The Materials Manager must be able to manage multiple tasks simultaneously and be able to communicate with other staff members.
What is hospital material management?
In a hospital, materials management is an important part of the overall function. It ensures that materials like planning, purchasing, store and inventory control, care and preservation, issue of materials, accounting and disposal of scrap are managed effectively.
What is material management in building construction?
Materials management is a critical function in any organization. By coordinating the purchase, transportation, storage and control of materials, organizations can reduce the wastage and maximize the profitability of their products.
What is the difference between material management and supply chain management?
Materials management is a vital part of any supply chain. By managing the materials used in production, companies can reduce their costs and improve their efficiency. In addition to reducing the amount of waste created, materials management can also help protect against spoilage and essential equipment failures.
Is material handler a good job?
Material Handler is responsible for handling all the materials that are used in a factory or business. They may be responsible for handling materials like paper, cardboard, and other cardboard products. They may also be responsible for handling materials like plastic and metal.
Is material handler hard?
"The job was okay. I didn't get paid very well, but it was physical work. The hours were short, but I could work overnight. The only problem was that the work was spread out over many shifts." - source.
What industry is material handler?
In the supply chain industry, material handlers move large numbers of goods to and from various storage and production areas. Some Material Handlers may specialize in moving specific types of non-hazardous items, like clothing and various consumer goods. The industry is constantly evolving as new technologies and innovations are developed, making it an ever-changing and lucrative business.
What are the 5 parts of a bill of materials?
The BOM for the new laptop is 12 GB, and it has a part number of Laptop_BAY24I. It includes a description of "A powerful and lightweight laptop for all your needs." The cost is $1,499.99. This laptop is expected to be in stock within the next few days.
What is Bill materials PDF?
A BOM is a document that describes the components and assembly of a product. It can help to identify which parts need to be ordered in order to produce the product. The BOM can also include information on the manufacturing process and how much time and money it will take to produce the product.
What is material coordination?
A material coordinator is responsible for managing the flow of materials and supplies. This position is commonly found in the construction, distribution and manufacturing sectors. The accurate and timely management of shipments is central to the cost-effective operation of businesses in these industries. The successful candidate will need to be able to organize material flows, manage inventories, and track shipments. They will also be able to communicate with clients and other departments on a daily basis.
Who is logistics coordinator?
The logistics coordinator is responsible for ensuring that products are delivered to their destination in a timely and effective manner. They work with the manufacturing company to ensure that all necessary parts are available and that products are received in an appropriate condition.
Why material management is important?
Material management is vital to ensure the flow of goods for production purposes to satisfy customer demand. It also ensures production schedules are met. Moreover, it can help save production costs while maintaining product quality.
What are the types of material management?
MaterialsRequirements Planning is one of the most important steps in material management. By knowing the right materials requirements, you can reduce your investment in materials by up to 60%. Additionally, by planning and controlling your supply chain, you can ensure that your materials arrive in good condition and at the planned quantities. Finally, quality control plays an important role in ensuring that all materials are used properly.
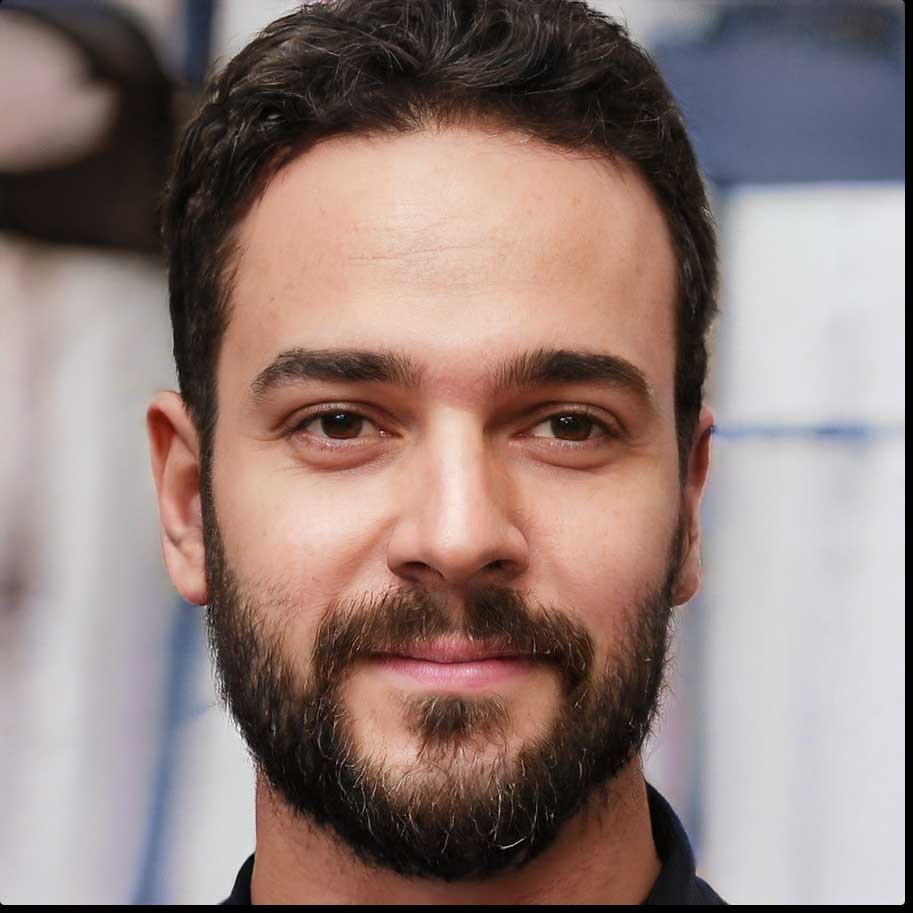
Warning: Undefined variable $post_category in /var/www/bestcareerguide.com/post.php on line 96
Category