MANUFACTURING COST ACCOUNTANT JOB DESCRIPTION
Find detail information about manufacturing cost accountant job description, duty and skills required for manufacturing cost accountant position.
What does a manufacturing cost accountant do?
Cost accountants complete gross margin analyses related to a company's products, inventory and its overall value. As an essential part of the accounting function, cost accountants calculate the costs of goods sold on the company's financial reports, which affects the company's bottom line. Goods sold on a company's financial reports are necessary to make informed decisions about where to allocate resources and what investments to make in order to achieve profitability. By understanding how these costs are incurred, cost accountants can make informed decisions that impact the overall health and viability of a business.
What is the role of cost accounting?
In accounting, cost accounting helps businesses accurately ascertain costs by using various techniques such as job costing and process costing. By using these techniques, businesses can identify the necessary expenses needed to cover the required tasks and projects. This information can then be used to better manage the business and make informed decisions about future costs.
What is FOH in accounting?
Factory overhead costs are the expenses incurred during the manufacturing process, not including the costs of direct labor and direct materials. This can add up to a large sum of money when it comes to businesses, so it is important to be aware of how much this cost can affect your bottom line.
What are examples of manufacturing costs?
The manufacturing overhead cost of a company can be significant. This includes costs related to repairs and maintenance, depreciation of the manufacturing equipment, utilities, salaries of manufacturing supervisors, and so on.
What are the three basic types of manufacturing costs?
Usually, manufacturing processes involve the use of a variety of materials and labor to complete a product. Direct materials are the most common, as they are directly involved in the manufacture of the product. For example, raw materials for a manufacturing process may include metals, plastics, and other materials that are used to make a product. Direct labor is also involved in manufacturing, but it is more often associated with tasks that do not require significant physical activity. For example, employees might print labels or assemble products. overhead costs are costs that are not directly related to the production of a product but are instead incurred by an organization as a whole. For example, wages and salaries may be spent on purchasing goods and services necessary for manufacturing or any other business entity.
What is cost accounting with example?
In business, fixed costs are expenses that are recurring regardless of the level of production. These costs can include rent, depreciation, interest on loans and lease expenses. This means that companies have to plan ahead for these costs and make sure they are covered each month.
What is cost accounting in simple words?
A company's cost structure can be broken down into three main categories: product costs, service costs, and business activities costs. Product costs include expenses related to making and selling products, such as research and development, manufacturing, and distribution. Service costs include employee salaries, wages, benefits, and transportation expenses. Business activities costs include general and administrative expenses such as marketing, advertising, and human resources management. These expenses are usually spread out over a longer period of time due to their size or complexity.
How do you calculate manufacturing cost?
It costs a lot of money to produce a product. The cost of raw materials and labor are the two main factors that contribute to manufacturing cost.
What is Prime cost accounting?
costs of a product can be divided into two categories: materials and labor. Materials cost is the price of the raw materials used to produce a product, such as metals or plastics. Labor cost is the amount of time and effort needed to complete a task, such as welding or fabricating products. When it comes to manufacturing products, costs often reflect how much money a company spends on raw materials and labor. For example, if a company spends $100 on metals for its product, then it must also spend $10 on labor to make that metal into a product. This means that the company has spent $110 in materials and $10 in labor costs for one product.
What is included in MOH?
In order to produce high-quality products, manufacturers often need to incur overhead costs. These costs can include the rent of the production building, property taxes and insurance on manufacturing facilities and equipment, communications systems and computers for a manufacturing facility, depreciation on manufacturing equipment, and salaries of maintenance personnel, as well as salaries of factory management team. However, there are many factors to consider when calculating these costs, so it is important to get accurate information.
Why is manufacturing costs important?
Manufacturing costs play an important role in the success of a product. By understanding the costings for different aspects of a product, designers can create products that are economically viable and have high added value.
What is the purpose of manufacturing cost?
Manufacturing costs are the expenses associated with making a product. They can be divided into two categories: production costs and marketing costs. Production costs include all of the expenses associated with manufacturing a product, such as wages, materials, and labor. Marketing costs include all of the expenses necessary to promote a product, such as advertising and distribution.
What is manufacturing cost in a company?
Manufacturing costs are the costs incurred during the production of a product. These costs include the costs of direct material, direct labor, and manufacturing overhead. The costs are typically presented in the income statement as separate line items. An entity incurs these costs during the production process.
What is manufacturing in accounting?
Manufacturing cost accounting encompasses the assessment of costs associated with producing goods and services. These costs can significantly impact profits and compliance with accounting standards.
What is accounting for manufacturing business?
Usually, when a business organization designs its accounting system, it strives to maximize profits. However, in the case of manufacturing businesses, there are additional considerations that must be made when calculating inventory valuation and cost of goods sold. For one, inventory may increase as production increases; this is due to the fact that more materials are needed to produce a product. In addition, it can take time for new products to reach market shelves, meaning that older products may need to be replaced sooner than initially planned. Further complicating matters is the fact that manufacturing businesses often sell goods in multiple channels - e.g., through distributors and retailers. This means that each of these entities might have different profit margins, which could lead to an underestimation of the value of inventory on a particular sales channel.
What are the types of manufacturing account?
6 most common types of Manufacturing accounts are raw materials, direct labor, overhead, work-in-process, finished goods, and cost of goods sold. Raw materials account for the majority of the cost of manufacturing products. Overhead costs include wages and salaries, marketing and distribution costs, and transportation costs. Work-in-process is the next largest cost type. This is when products are being created from scratch and includes everything from designing to manufacturing. The final cost includes the prices paid for raw materials and labor. Finally, overhead costs include plant depreciation, interest on debt, and other miscellaneous expenses.
What are the 3 types of cost accounting?
Standard costing is a method of accounting that uses standard units of measure to calculate costs. This method is often used in businesses where there are many different types of products or services being produced. Standard costing allows for multiple comparisons of costs to determine which method is the best suited for the particular business. Activity-based costing is a form of standard costing that uses activity data to calculate costs. This method can be used in businesses that have a lot of different types of tasks that need to be completed simultaneously. Activity-based costing allows for multiple comparisons of costs to determine which method is the best suited for the particular business. Lean accounting is a type of activity-based costing that uses lean methods to calculate costs. Lean accounting can be used in businesses that have a lot of different types of tasks that need to be completed simultaneously, but it can also be used in businesses that do not have a lot of activity data. Lean accounting allows for multiple comparisons of costs to determine which method is the best suited for the particular business. Marginalcosting is another type of cost accounting that uses marginal data to calculate costs. Marginal costing can be used in businesses that have a lot of different types of tasks that need to be completed simultaneously
How hard is cost accounting class?
In cost accounting, cost is the measure of the total cost of a product or service. Cost can be in terms of money (e.g., cash), products (e.g., production costs), or services (e.g., marketing costs).
How do you get into cost accounting?
Cost Accountant jobs are becoming more and more popular, as the demand for their services grows. With a degree in accounting or related field, cost accountants can thrive in any economy. In today's economy, businesses are constantly looking for ways to save money and cut costs. This is where a cost accountant comes in - they can help your business figure out how to make the most of its resources. If you're interested in being a part of an industry that's constantly growing and changing, cost accountancy may be the perfect career for you. As businesses increasingly look for new ways to save money, the need for cost accountants will only continue to increase. So if you're thinking about a career change - Cost Accountant may just be the right choice!
Is costing and cost accounting same?
Cost accounting is the process of determining the cost of a product, but it is also a technique used to assist the management or business in making budgets and standards. By understanding the costs associated with different aspects of a product, businesses can make more informed decisions about which products to produce and how much money to spend on them. This knowledge can help them to avoid overspending and underinvesting, which can lead to financial problems down the line.
What are cost accounting tools?
A cost accountant uses a variety of tools to analyze costs, including job costing, process costing, standard costing, activity-based costing, throughput analysis, and direct costing. By understanding the cost patterns of various businesses, the accountant can provide valuable information for making informed decisions about cost structure and budgeting.
What are the 10 objectives of cost accounting?
It is important to understand the objectives of cost accounting, especially in the context of advertisements. By controlling costs, a business can reduce its overall costs and improve its financial performance. Additionally, it is important to determine the selling price for an product or service and use this information to make decisions about marketing and business strategy.
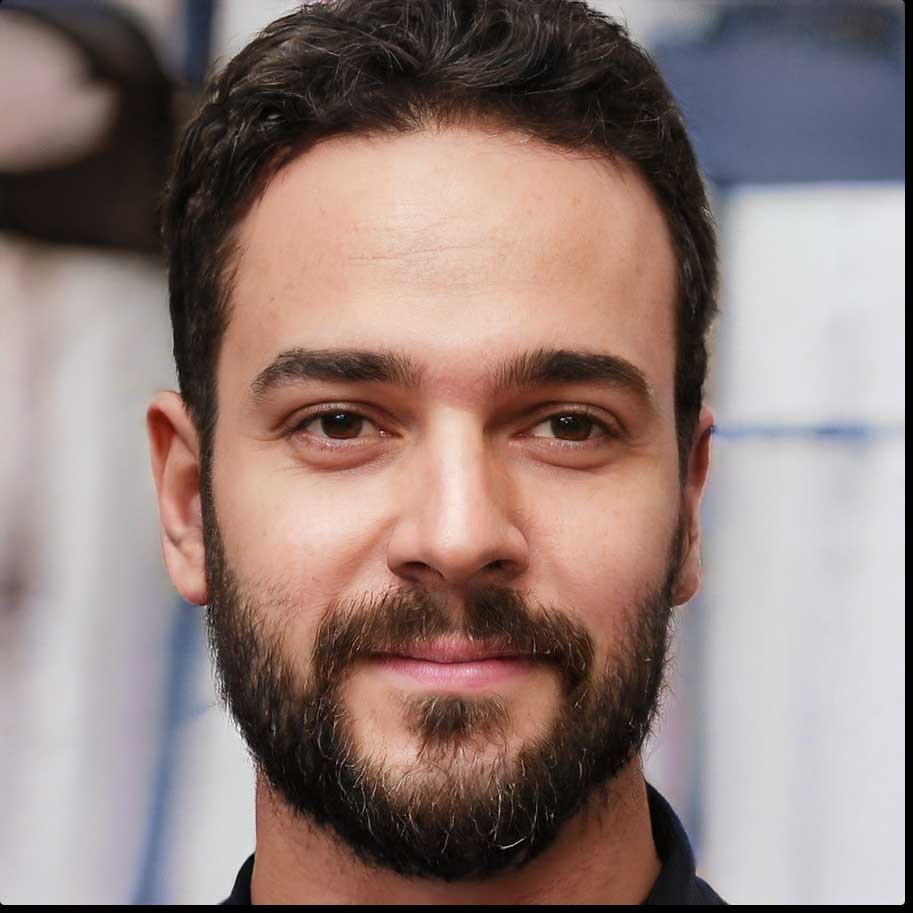
Warning: Undefined variable $post_category in /var/www/bestcareerguide.com/post.php on line 96
Category