DIRECTOR QUALITY SYSTEM JOB DESCRIPTION
Find detail information about director quality system job description, duty and skills required for director quality system position.
What does a director of Quality Systems do?
It is the responsibility of the Director of Quality Control to develop, implement, and periodically evaluate a program to ensure the organizations production operations, from raw materials to finished products, meet the quality, integrity, and efficiency standards set by the organization. The program will include reviews of production processes and materials handling techniques. The Director will also review any potential issues that may occur in the production process. If any issues are found, they will be addressed and corrected.
What does a director of quality improvement do?
As the director of quality improvement, your job includes collaborating with management to develop quality assurance plans, working with employees to implement the strategies, reviewing documents for accuracy, and monitoring client satisfaction. In addition to these tasks, you will also be responsible for developing and implementing quality assurance plans for new or revised products.
What does director of quality and compliance do?
It is the Director of Quality and Compliance's responsibility to ensure that all patient care services are delivered in a safe and high quality manner. This includes but is not limited to, creating and implementing quality control measures, ensuring that patients are treated with respect and dignity, and protecting the safety of the staff. The Director of Quality and Compliance is responsible for many different areas within the company. They work with their team to create plans that ensure that all patient care services are delivered in a safe, high quality manner. They also work with their team to protect the safety of their employees. By working together, they can ensure that the patients receive the best possible care without any negative consequences.
What is a quality systems officer?
The development of induction documents for a company is an important part of the quality system process. The documents must be accurate and up-to-date, and ensure that corporate induction requirements are adhered to. The quality system principles and knowledge must be communicated to all employees, so that they can understand and take advantage of the system.
How do you become a director of QA?
A quality assurance director is responsible for ensuring the quality of products and services. They must have a degree in an appropriate field and experience with QA measuring and testing equipment. Additionally, they must have working knowledge of safety requirements and legal standards. A quality assurance director should be able to create effective Quality Assurance Director job descriptions.
How can I be a good quality director?
It is not easy to be a successful director. There are many challenges that come with the job, but the ability to apply your creative skills and experience in a variety of boardroom scenarios is essential. Directors have to have good judgment, communication skills, and active contributors, as well as integrity and honesty. They also need to be intelligent and curious, with a genuine interest in their work.
What is a director of quality management?
A quality management director is responsible for directing all quality management activities of an organization. They develop strategic plans and policies for improving quality and work with top management to ensure compliance with regulatory agencies. A key role of a quality management director is to ensure that all products, services, and processes meet the required standards.
What are quality control skills?
Quality control standards and legal standards are important to ensure the quality of products. The knowledge and skills required for this task include understanding data, mathematics, and statistical techniques, as well as having previous experience in manufacturing and production processes. These skills are important in ensuring that products meet legal standards, which are important for safety reasons.
What is meant by quality system?
A quality system is a structure for managing the quality of the output of a manufacturer. They have a very strict quality system for inspecting items and delivering the best products. A good quality system prevents errors from occurring rather than correcting them after they have occurred.
How do I become a quality control system manager?
Crystal City is a city in Virginia that was founded in 1781. The city is known for its manufacturing and production industries, including the production of glass and metals. The city has a population of over 125,000 people. Crystal City is a great place to live and work.
What are the responsibilities of management in quality system management?
The management should fix responsibility and authority of every employee to control and detect nonconformity affecting quality. This will help to prevent quality issues from happening in the future.
What I would do if I was the quality assurance QA director?
A quality assurance director oversees all aspects of product delivery and ensures that high-quality products are delivered on time and within budget. They work with internal partners whose responsibilities relate to compliance and production. Directors play an important role in ensuring that product quality is maintained, which can lead to reduced costs and improved customer satisfaction.
How long does it take to become a QA manager?
Quality assurance managers are responsible for ensuring that products and services meet specific quality expectations. They work closely with customers, partners, and other departments to ensure that all products and services are delivered in an accurate and timely manner. This position can be a challenging but rewarding job. As a quality assurance manager, you will be responsible for ensuring that all products and services are delivered in an accurate and timely manner. You will also be responsible for developing policies and procedures to ensure that these expectations are met. This position can be a rewarding experience if you have the skills necessary to manage projects successfully.
What are careers in quality assurance?
Quality assurance professionals work together to create a process for creating and testing products before release or production. The purpose of QA is to ensure each product or service a company produces is uniform and meets certain standards. The QA process begins with the development of a product plan. This document establishes what the product will include and how it will be tested. Next, the team creates a quality assurance program. This plan outlines how products will be tested and how they will be released. Finally, the team creates an acceptance test plan. This document outlines how tests will be conducted to ensure that the product meets specific requirements.
What skills are needed for a director?
No matter what your job may be, there are a few things that you'll always need in order to succeed. One of those things is a strong writing ability, as it can help you to communicate your ideas effectively and efficiently. You also need to be able to think on your feet and come up with creative solutions when it comes to problems. Finally, you'll need the ability to lead a team, as this can be a difficult task if you don't have charisma and the ability to motivate people.
What are the key skills of a director?
She is a highly experienced, senior leadership and people management expert who has worked in a number of industries. She has a deep understanding of how to lead and manage teams, develop strategies and make decisions quickly. She also has experience in accounting, finance and risk management.
How much do directors make?
In recent years, film directors have become increasingly popular. They can earn a lot of money, depending on the project they work on. New directors usually make more than experienced directors. Studios often pay these directors a large salary, as well as a percentage of the box office profits.
What is the highest position in the company?
When it comes to running a company, the CEO is the head of all C-level members and their report only goes to the board of directors. The CEO is responsible for overall strategy and operations, as well as day-to-day operations. They also have a huge impact on company culture and what people believe about the company.
Is managing director the same as CEO?
A CEO is the highest-ranking superior at a company. They are responsible for the company's public image and ensure that everything runs as efficiently as possible. A managing director manages the company day-to-day operations and ensures everything runs as smoothly as possible.
What are 4 types of quality control?
There are several methods of quality control, including an x-bar chart, Six Sigma, 100% inspection mode, and the Taguchi Method. The Taguchi Method is a reliable way to measure the quality of products. This method requires measuring how much each part of the product is different from the standard.
Is quality control a good career?
In the manufacturing industry, quality control and assurance are essential duties that employees need to take on. People working in this field need to be detail-oriented, able to communicate well, and have problem-solving skills.
What are the top 3 qualities required for QA?
A quality assurance manager is responsible for ensuring that products or services are of high quality and meet the needs of their customers. They must be skilled in leadership, organizational planning, communication, and problem-solving. MUbee has a number of regions where QASM may be required depending on the product or service being created.
What is an example of a quality system?
The quality management system (QMS) of a company is an important tool that helps to ensure that the products and services it provides are of high quality. The QMS includes systems to manage the quality of products and to ensure that they meet customer expectations. The system can also be used to monitor the progress of production and to identify any potential problems.
What is need for quality system?
A quality management system (QMS) is a system in place to ensure that the products and services that an organization provides are of high quality. Benefits of having a QMS include meeting customer requirements and instilling confidence in the organization so that it can lead to more customers, more sales, and more repeat business. A QMS can be costly to implement, but it has a significant impact on an organization's performance.
What are the 6 quality systems?
Inspection model 6 refers to the six systems that make up the company's overall operation: quality, production, facilities and equipment, laboratory controls, materials, and packaging and labeling. These areas are important to keep in mind when commenting on the company's performance, as they can affect the overall quality of its products.
What degree do you need for quality control?
Entry-level quality control inspectors should have at least a high school diploma or equivalent. Having a bachelor's or associate degree in quality assurance can expand a quality control inspector's job opportunities and increase their earning potential.
What is the primary focus of a quality management system?
Usually, quality management refers to the process of ensuring that products or services meet customer requirements and expectations. This can be done in a number of ways, including by monitoring and reviewing products and services regularly, setting rigorous quality criteria, and enforcing standards. Successful quality management is often based on a strong team effort that utilizes a variety of methods and techniques. By understanding the customer's needs, creating an effective system for tracking progress, maintaining communication with stakeholders, and developing procedures for dealing with problems ? all of which are crucial in ensuring success ? you can ensure that your customers remain confident in your ability to meet their expectations.
What is true of a quality system?
A quality system is a blueprint for how your business will work, identifying your business model and processes, and establishing specifications for performance. This system can help you tell if you're on track or not.
What are the benefits of quality management system?
A quality management system (QMS) is a system of control and communication used in the manufacturing and service industries to ensure the quality of products and services. A QMS provides a means for ensuring that key business processes are ran consistently and efficiently, while also providing an understanding of customer needs. By regulating successful working practices, QMSs can increase safety and reduce waste. Additionally, employees are more likely to understand their role in the system and be more motivated to achieve high standards. Overall, a QMS can provide significant benefits for businesses of all sizes.
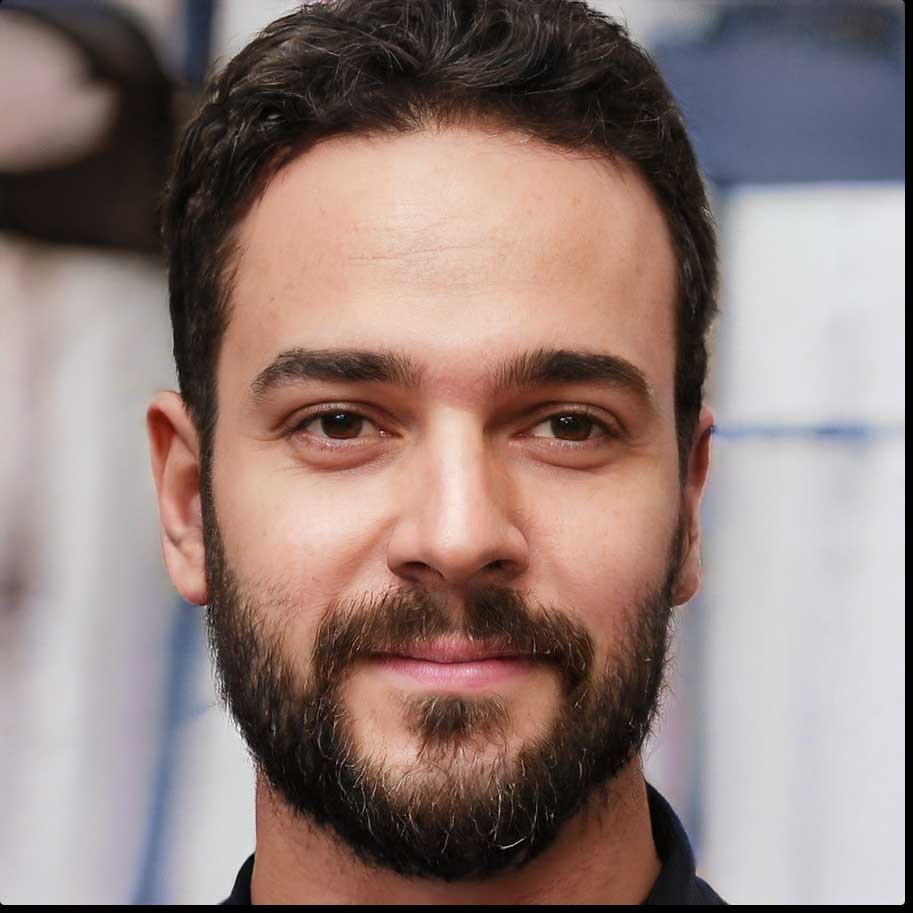
Warning: Undefined variable $post_category in /var/www/bestcareerguide.com/post.php on line 96
Category